As we all know, now more and more people are pursuing personalized differences, so personalization needs to make something different, that is, private customization. Private customization is particularly prominent in the gift industry, and gift giving, promotion and advertising have become commonplace. So today's editor will talk about the process of private customization of gifts?
Gift customization is actually a very complex and detailed process. So how can these personalized ideas or logos be presented on the product?
Due to the different types and materials of gift customization, the size of LOGO is different, and the gift color is colorful. Therefore, in the gift customization, we should select the specific printing process according to the situation.
There are three common processes of customized gifts: printing, hot stamping and laser engraving.
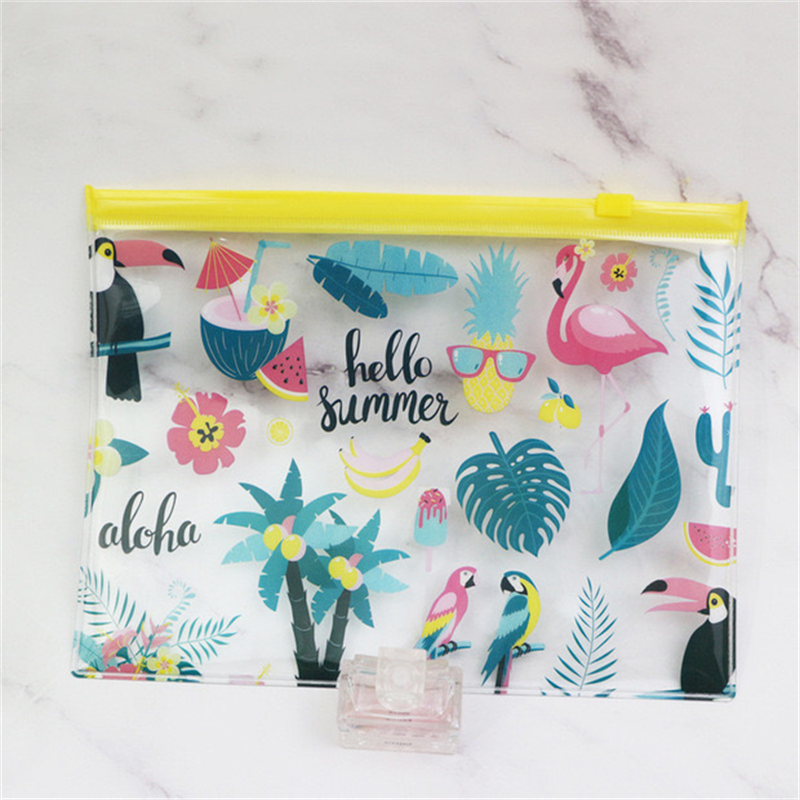
1、 Printing process
Common printing processes include screen printing, heat transfer printing, water transfer printing, color printing, etc.
1) Screen printing
Screen printing belongs to hole printing. That is, when printing, the printing plate transfers the ink to the gift surface through the hole of the hole plate through a certain pressure to form an image or text. Advantage
The plate making is convenient, the price is cheap, and the cost of batch printing is easy to control. Applicable to LOGO composed of 1-4 different colors It is especially suitable for those with small quantity and thick ink color. It is not limited by the texture of the bearing products, and the imprinting force is small; Strong light resistance, not easy to fade; With strong adhesion, the printed pattern is more three-dimensional.
Inferiority
Screen printing is only suitable for patterns with single color, simple transition color, color gradient effect or too rich color.
Scope of application
Paper, plastic, wood products, handicrafts, metal products, signs, knitwear, cloth, towels, shirts, leather products, electronic products, etc
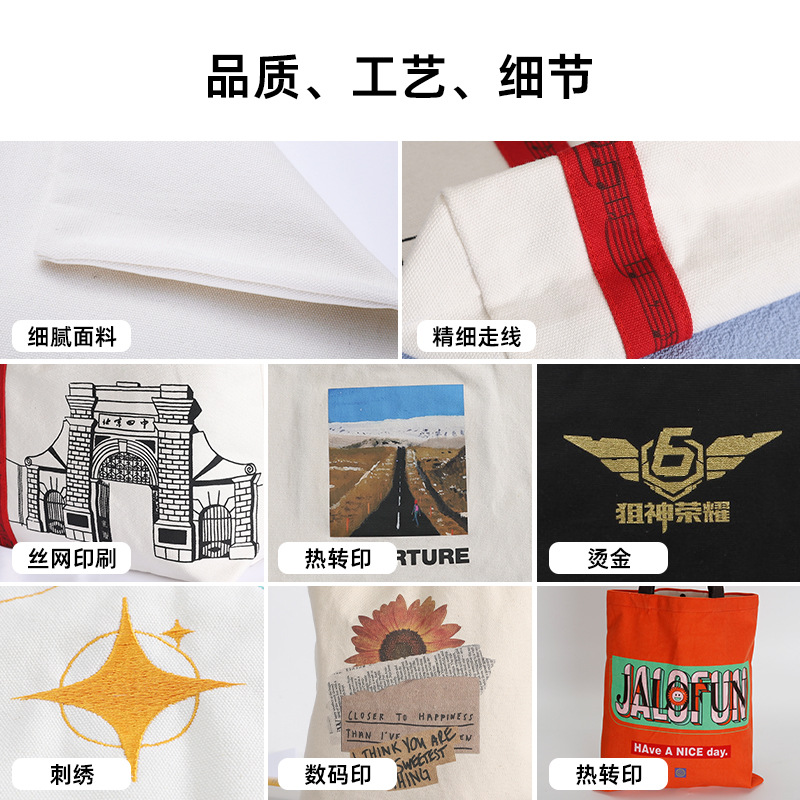
2) Heat transfer printing
Thermal transfer printing is divided into two parts: transfer film printing and transfer processing. The transfer film printing adopts dot printing (resolution up to 300 dpi), and the patterns are pre-printed on the film surface. The printed patterns are rich in layers, bright in color, ever-changing, small in color difference, and good in reproducibility, which can meet the requirements of the designers and are suitable for mass production; The transfer process transfers the exquisite patterns on the transfer film onto the product surface through a heat transfer machine (heating and pressurizing). After forming, the ink layer and the product surface are integrated, lifelike and beautiful, greatly improving the quality of the product.
Advantages:
Simple printing: it does not need the steps of plate making, plate printing and repeated color registration, and does not need various types of tools and materials required by screen printing and heat transfer.
No damage: it can be printed not only on tough crystal, stone, metal, glass and other materials, but also on soft leather, cloth, cotton and other materials; It can be printed on inorganic matter, or on organic matter with complex and changeable components.
Accurate position: avoid the problem of position deviation encountered in manual printing.
Disadvantages:
Professional thermal transfer equipment is required. For ceramic, metal and other items, thermal transfer coating is required on the surface.
First The design feels a little stiff and has poor air permeability. It will become soft after washing, but the air permeability is still relatively poor.
Second When the heat transfer T-shirt is pulled horizontally, the pattern will have small cracks corresponding to the fabric fiber. This is caused by the characteristics of heat transfer printing itself and cannot be avoided.
Third The color of T-shirt will change after hot pressing, such as white will turn yellow. This is caused by the evaporation of water in the T-shirt
Fourth Thermal transfer printing uses thermal sublimation ink to print the picture on the transfer paper first, and then transfer it to the surface of the medium. There are several problems that are difficult to solve: color deviation and positioning deviation. The picture of the finished product is also relatively easy to scrape off, and the fastness is poor. Generally, a protective film needs to be sprayed. In addition, flexographic printing is also required for transfer printing of special media.
Fifth Skilled printer with many years of experience is required.
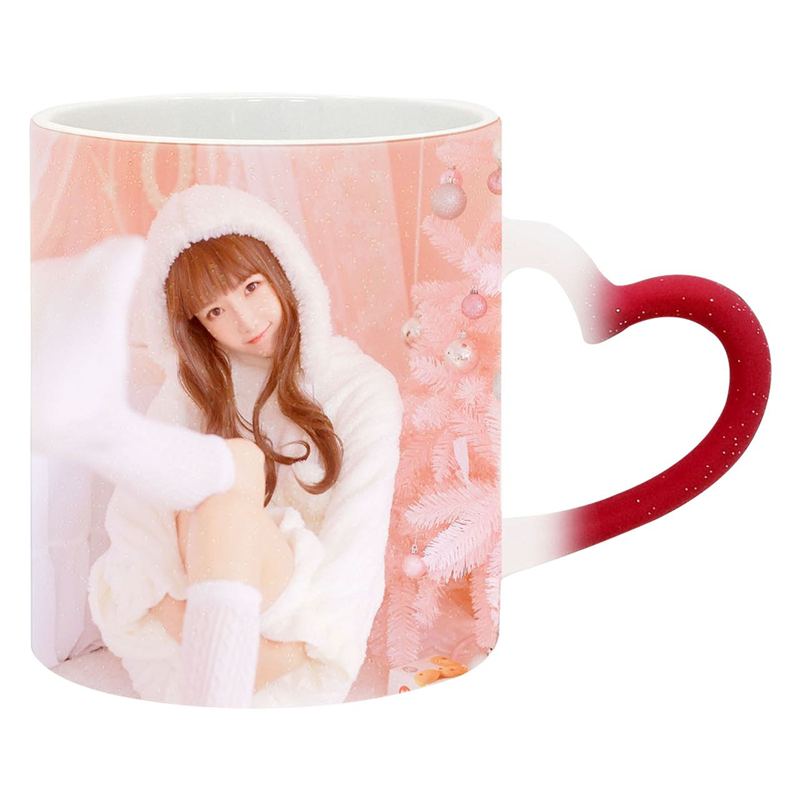
3) Water transfer printing
Water transfer printing technology is a kind of printing that uses water pressure to hydrolyze the transfer paper/plastic film with color patterns. With the improvement of people's requirements for product packaging and decoration, water transfer printing is used more and more widely. The principle of indirect printing and perfect printing effect have solved the problems of surface decoration of many products.
4) Color printing
Color printing is a process that uses different color plates on the same page to print several times to achieve color picture effect and transfer ink to the surface of paper, fabric, leather and other materials.
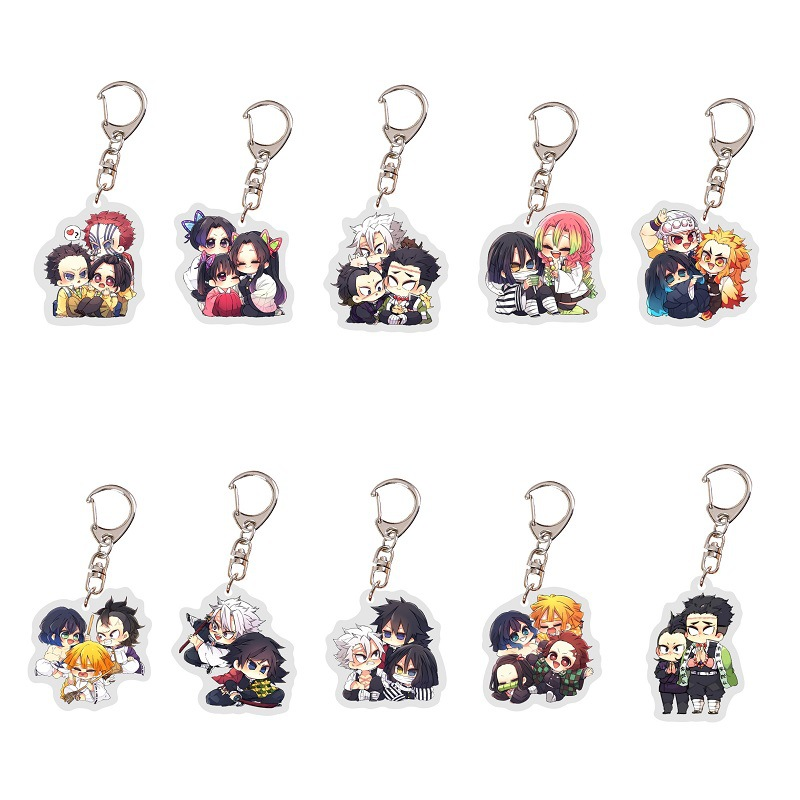
2、 Hot stamping process
Hot stamping is also called stamping. It refers to the process that the paper or leather gift parts are ironed with words and patterns of materials such as color foil, or embossed with various convex and concave LOGO or patterns by hot pressing.
Advantage
The design is clear, the surface is smooth and flat, the lines are straight and beautiful, the colors are bright and dazzling, and there is a sense of modernity; Wear-resistant and weather-resistant, special edition can be customized according to specific requirements.
Inferiority
The disadvantage of hot embossing is that it needs high temperature and high pressure, and even under high temperature and high pressure for a long time, some patterns can not completely fill the seal cavity.
Scope of application
Hot stamping is generally used in paper, textiles, leather and other gift packaging. Gift box bronzing, cigarette, wine, clothing trademark bronzing, greeting card, invitation card, pen bronzing, etc.
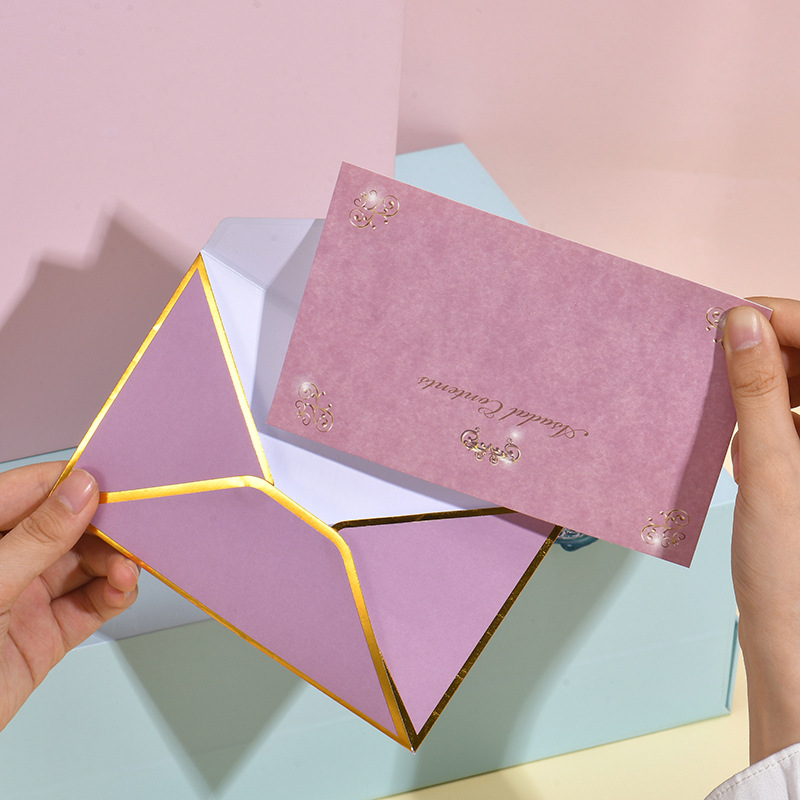
3、 Laser engraving (metal and non-metal)
Laser engraving is the physical denaturation of instant melting and vaporization under the irradiation of laser engraving to achieve the purpose of processing. Laser engraving is the use of laser technology to carve words on objects. The words carved by this technology are not scored, the surface of the object is still smooth, and the handwriting will not be worn. Of course, different laser marking machines will print different materials. Customers can choose the appropriate model according to their needs.
Laser lettering is also a relatively simple process, which is suitable for a single product, a small number of products and a batch of products. It is particularly important in private customization, and the disadvantage is that the color is relatively single. Black and white or metal color.
Laser equipment includes: fiber laser marking machine, carbon dioxide laser marking machine, ultraviolet laser marking machine
Advantage
Strong sense of technology, no contact, no cutting force, small thermal impact; The marks carved by laser are fine, and the lines can reach the order of millimeter to micrometer. It is very difficult to copy and change the marks made by laser marking technology.
Scope of application:
Wood products, plexiglass, metal plate, glass, stone, crystal, paper, two-color plate, aluminum oxide, leather, resin, spray metal, etc.
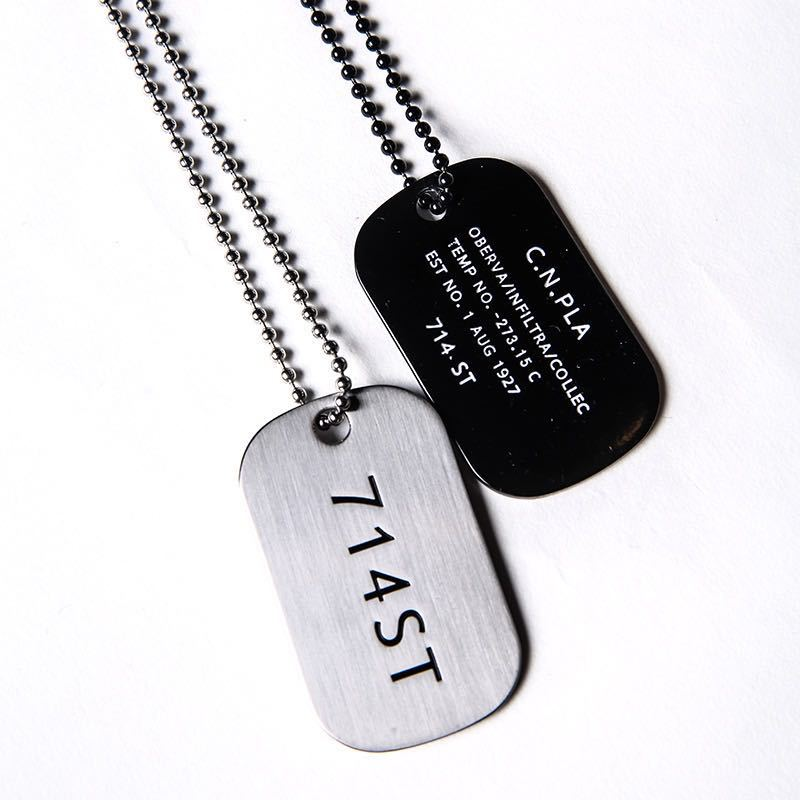
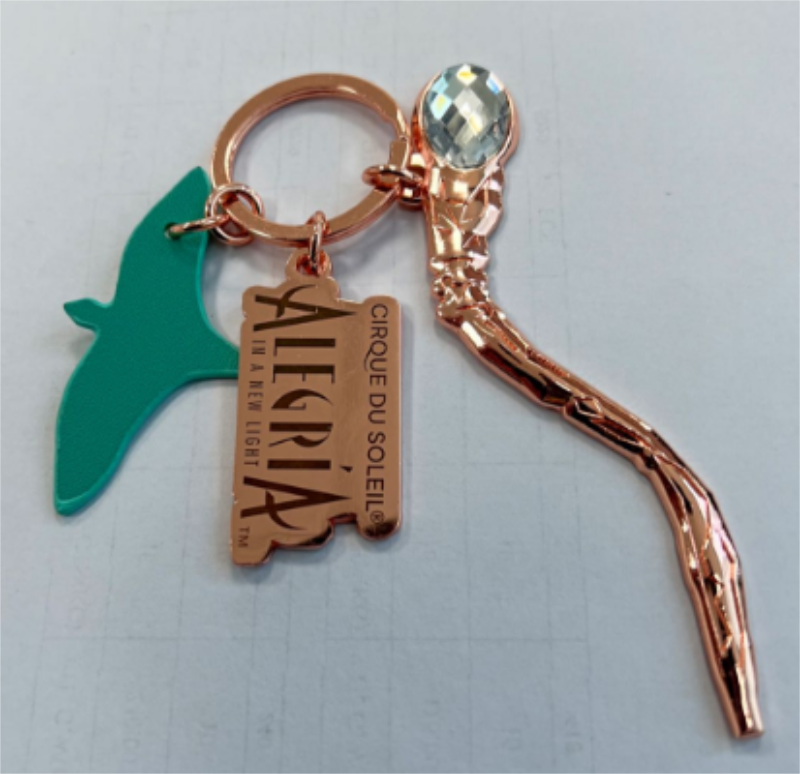
Post time: Jan-30-2023